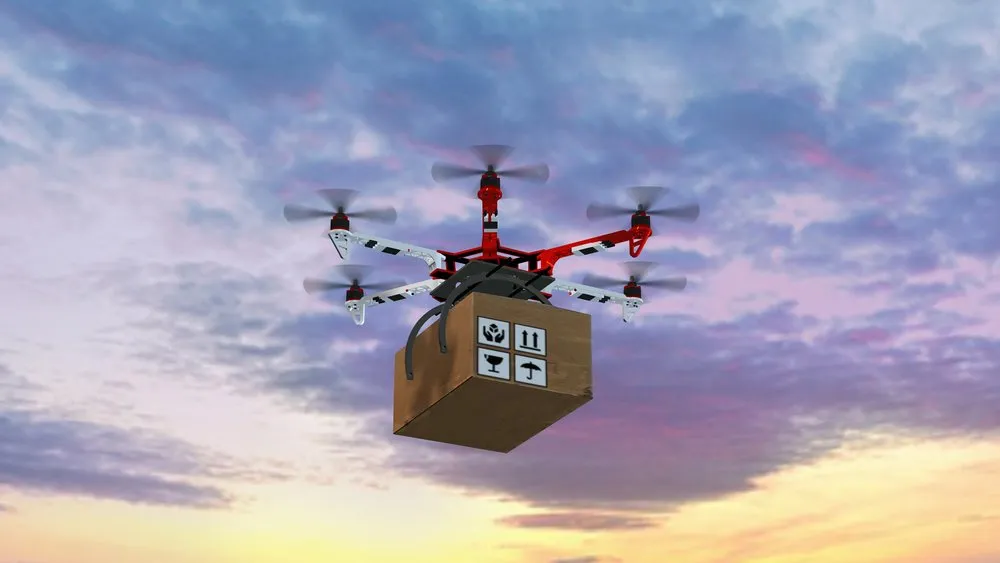
There may come a time when flying drones and automated robots make the human warehouse worker obsolete. In fact, this is a fear that pervades many companies across a variety of industries. But based on what we’re seeing in this field, that time is still a ways away, and in many instances drones and robots are making lives easier for those in the warehouse.
At the moment, the warehouse is really the best place for these machines. Though Amazon, for example, has spoken about the possibility of a drone delivery system that could drop packages off at a customer’s front door, that reality is not logistically, economically, or legally feasible at this point. Drones are still a behind-the-scenes kind of tool in the supply chain—which for warehouses means they’re on the front lines.
There are a few notable drone and robot trends to monitor in this space. Let’s examine how machines can make life in the warehouse less taxing, more efficient, and more cost-effective—depending on how much of an investment each company wants to make.
Better asset location and cycle counting
Arguably the optimal use for drones in the warehouse at this point in time is in inventory and asset management. Traditionally, tracking the amount of inventory a warehouse had on-hand, or the status of fixed assets like vehicles and computers in terms of their maintenance or
tax depreciation schedule, was done onerously, by hand. In recent years,
many companies have upgraded to using barcode or RFID technology as part of a larger asset tracking system, which updates records in the database seamlessly and across all devices.

But even using superior technology has created dilemmas for warehouses to solve. A recent
article in Forbes describes a recent asset tracking issue facing automotive company Daimler, and how drone tech company PINC Solutions helped address it:
Daimler was looking for a solution for tracking finished vehicles, which are packed very tightly in large yards. In fact, with vehicles packed bumper to bumper, you could not read the vehicles RFID tags that were packed in the middle. Thus, was born their drone business. Drones can read vehicle IDs of Daimler cars or trucks in the middle of a line of vehicles.
PINC drones can be used to scan barcodes or RFID tags in positions that are literally impossible for workers to get to when assets were packed tightly. There are times when taking stock of inventory isn’t necessarily impossible — just time-consuming and challenging. Consider another dilemma addressed by drones in the warehouse:
Mr. Piro pointed out that when a full cycle count (i.e., checking to see that inventory the system says is located in certain slots is really there) is done, it can require 10-15 people and checking high slots can be difficult. PINC clearly believes automating this can have good payback as drones can find lost pallets and slots that are supposedly full but are currently empty.
These are two of the major issues with traditional, manual inventory management: It takes an exorbitant amount of time and is often wrong. Machines are virtually incapable of making these accounting errors if programmed correctly, and they do so with, pardon the phrase, machine-like efficiency. And they do so under the supervision and care of warehouse workers, who no long have to spend long hours doing arduous busy work.
Continuous inventory
Here’s another issue that we may never have considered before the advent of machines: For the most part, work only gets done during work hours. Warehouse workers can only be on-site so many hours each day, and even if a warehouse was to run around-the-clock, there would be slight drops in efficiency as the hours wore on, breaks were taken, and human fatigue became a factor.
At the moment, many drones are piloted by warehouse workers during their shifts, used to reach difficult areas and to otherwise facilitate tracking. But there will come a time when “continuous inventory” will be possible. By the usual definition,
continuous or perpetual inventory review is when a system updates inventory counts each time any item is removed from inventory (as opposed to a periodic system, when the database is updated on a schedule).
Imagine a system that is not only constantly updating—which systems built on barcode scanners typically do anyway—but is operating around the clock. Drones could be scanning the inventory of a massive warehouse (like
the ones Amazon uses to fulfill orders) overnight, returning themselves to charging stations when necessary. Those hours might be best for
claims and returns, resetting inventory for the next day’s work, and can prepare the warehouse for the next work day while the workers themselves get some sleep.
Tiny drones are the way of the future
There are lots of reasons why drones are not already taking over warehouses—cost and investment being at the top of the list (more on that below). Any reason is that many warehouses were not built with drones in mind, and aren’t designed to allow for seamless barcode scanning by flying objects. As noted by the Forbes article:
A current limitation of using drones for cycle counting is that it really can’t see inventory stacked behind other inventory in a slot. This means it is great for one deep pallet racks, but cannot do the full cycle count in other types of slotting situations.
What’s the answer to this? According to PINC, one answer is almost too obvious for words: Smaller drones. Like, extremely small—insect-sized, perhaps. Small drones that can operate in a variety of spaces (and don’t require companies to completely overhaul the way they store their inventory and assets) are the solution to unwieldy pallets and other traditional means of storage, and they’re hardly the stuff of science fiction.
They’re already among us, in fact.
What is the ROI for this?
Of course, one of the major questions for any company involved in warehousing is whether drones will be worth the investment for them. There are still plenty of companies who don’t do any sort of automated inventory or asset management, presumably out of a combination of ignorance and return on investment questions.
The truth is, highly automated warehouses are expensive, and will likely take anywhere from five to ten years to see any ROI. Some companies—mainly big businesses like Amazon, Wal-Mart and Target—can afford that kind of wait. Small- and mid-sized companies can’t.
But that’s exactly what makes robots and drones so appealing: They are scalable and flexible. Businesses can purchase a handful of them, try them out in one area (say, just fixed asset management), see how it works and go from there. They are hardly static and can usually be integrated into existing systems with limited additional investment in time and money. They can be warehouse helpers — assisting in scanning hard-to-reach places, or to join in the overall effort—rather than immediately commence in the takeover. Panelists at
a recent conference covered by Forbes cited instances of companies going under due to failed automation projects that aimed to overhaul the way the supply chain worked.
So if you’re a business owner who needs to balance both efficiency and company culture (i.e., you’re not prepared for a warehouse without workers), who wants to see what technological advancements like flying machines can offer the company but doesn’t want to commit fully just yet, drones and robots that focus on inventory and asset management are a great place to start.
The drones role in the workplace is just beginning—it’s better to embrace them and see what kind of ROI they offer than to shun altogether.